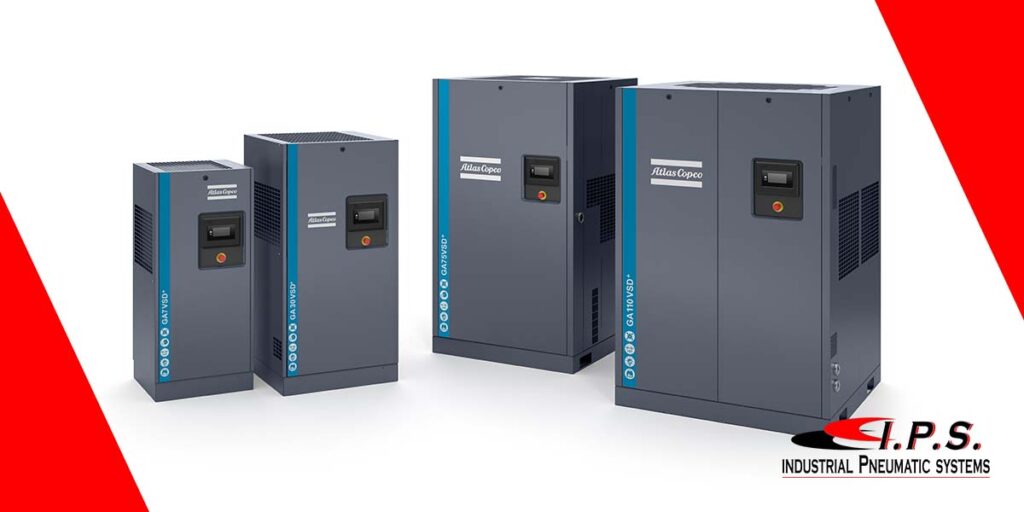
Air compressors are crucial for various industries, including food, manufacturing, automotive and healthcare. This equipment powers tools and other equipment essential for routine applications. However, different air compressors have varying pressure capacities, duty cycles and air quality considerations. Understanding these elements will help you learn how to choose an air compressor.
Types of Air Compressors
There are several types of industrial air compressors, which suit specific applications and requirements. Specific types of air compressors to note include:
- Rotary screw compressors: These compressors are common for stationary applications in manufacturing, public works, automotive, food and beverage processing, and more. Rotary screw compressors deliver a continuous duty cycle, do not require an air receiver tank and are compact. You can find fixed-speed rotary screw compressors and variable-speed drive models to meet your needs and budget. Many rotary screw compressors can also integrate dryers for dry, clean air.
- Piston compressors: Piston or reciprocating air compressors are common in light manufacturing facilities and machine and tire shops. Suitable for intermittent use, piston compressors typically work between 50% to 60% of their duty cycle, or about 30 to 35 minutes an hour. Piston compressors also require cooling periods between run cycles to avoid breakage or overheating.
- Oil-injected compressors: These compressors use oil as lubrication to reduce friction and complete cooling processes. Although oil-injected compressors can meet many pressure and capacity requirements, the process results in compressed air with slight traces of oil contamination. This may be unsuitable for sensitive applications, such as those in pharmaceutical or food processing, that require extremely high air purity.
- Oil-free air compressors: An oil-free air compressor does not require oil for lubrication. The lack of oil reduces the likelihood of contamination, which is crucial for industries like food and beverage. You can find piston and rotary screw compressors in oil-injected or oil-free varieties.
How to Pick the Correct Air Compressor
When compressed air is critical for your applications, it is essential to choose the right equipment. Consider these factors to help narrow down your air compressor selection:
Compressor Capacity and Flow Rate
Capacity refers to the total air volume a compressor can hold, while flow rate indicates the air volume a compressor can deliver each minute. Gallons or liters often depict the capacity, and CFM measurements indicate the flow rate. Manufacturer data sheets can help you identify these measurements. However, a professional compressed air audit can ensure the most accurate measurements for your needs.
Generally, reciprocating compressors are more suitable for lower flow capacities, while rotary screw compressors offer higher flow capacities. As a general rule of thumb, choose an air compressor with a safety margin of up to about 30% to avoid constantly running your compressor at maximum capacity.
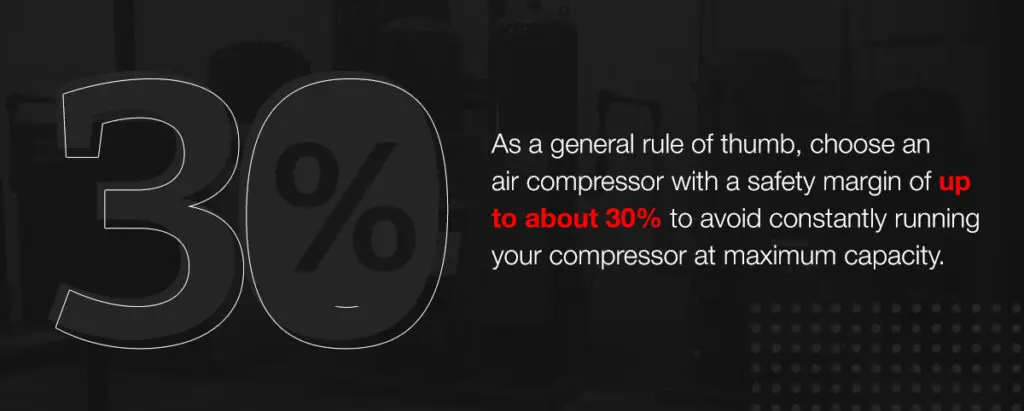
Pressure Requirements
Pressure is the amount of force your equipment needs to perform at any point in time. Pressure, typically indicated by psi, is a crucial consideration. If the pressure is too low, the compressor may not be able to power equipment or complete tasks properly. Consider these common air compressor applications and their pressure requirements:
- Sandblasting applications typically need between 70 and 90 psi.
- Power tools often operate with 90 to 120 psi.
- HVAC systems need 80 to 100 psi.
- Refrigeration generally needs 60 to 80 psi.
- Automotive assembly applications often rely on 90 to 120 psi.
- Food and beverage packaging often ranges from 70 to 90 psi.
Maintenance Needs
Air compressor maintenance is crucial for ensuring reliability, efficiency and longevity. Every compressor requires some maintenance, but demands vary greatly by type. Basic maintenance includes changing filters, replacing oil and requesting routine inspections.
Depending on the specific type you select, you may have additional daily, weekly or monthly maintenance requirements. For example, rotary screw compressors require daily temperature and oil level checks. Additionally, electric compressors will require power cord inspections, while gas compressors require spark plug and fuel line inspections.
It is critical to understand your compressor’s maintenance requirements and choose a compressor that aligns with your objectives. If you need a continuous compressed air supply, choosing equipment with frequent maintenance needs can be counterproductive and result in unwanted downtime.
Oil-Injected vs. Oil-Free Air Compressors
Choosing the correct air compressor requires considering the differences between oil-injected and oil-free models. For some industries, such as healthcare, oil-free compressors are crucial for minimizing contaminant exposure. However, both types have their advantages and considerations.
Oil-injected compressors are common in industrial facilities, small workshops and manufacturing applications. These models use oil to cool, seal and lubricate compressed air. Slight contamination does occur from this process, but it does not hinder compressor performance. You can also use carbon-activated filters to provide additional cleaning and achieve higher air purity without the larger investment of an oil-free model.
Industries that must avoid contamination, such as food and beverage, pharmaceuticals, and electronics manufacturing, require an oil-free setup. Oil-free compressors are typically more expensive because they use alternative cooling methods. These models can also have higher maintenance costs since they experience more friction.
Air Purity Classes
Compressed air adheres to unique International Organization for Standardization (ISO) ratings. Understanding ISO ratings and your air purity needs is a crucial consideration when choosing an air compressor. Air compressors can range from ISO 8573-1 Class 0 to Class 5, with air purity diminishing for higher rankings.
Class 0 is the cleanest choice, as equipment can guarantee 100% oil-free air. These models are common in food and beverage, chemical, and medical applications where contamination can severely impact products or processes. These compressors can have high price points, but are the safest option for sensitive applications.
One important note is the difference between Class 0 compressors and “technically oil-free” compressors. “Technically oil-free” compressors use filters, but their marketing can be misleading, suggesting a level of air purity that may not be accurate. Carefully assess your air quality requirements and verify that the chosen compressor actually delivers the necessary purity to prevent inadvertent damage to your compressor, tools and other equipment.
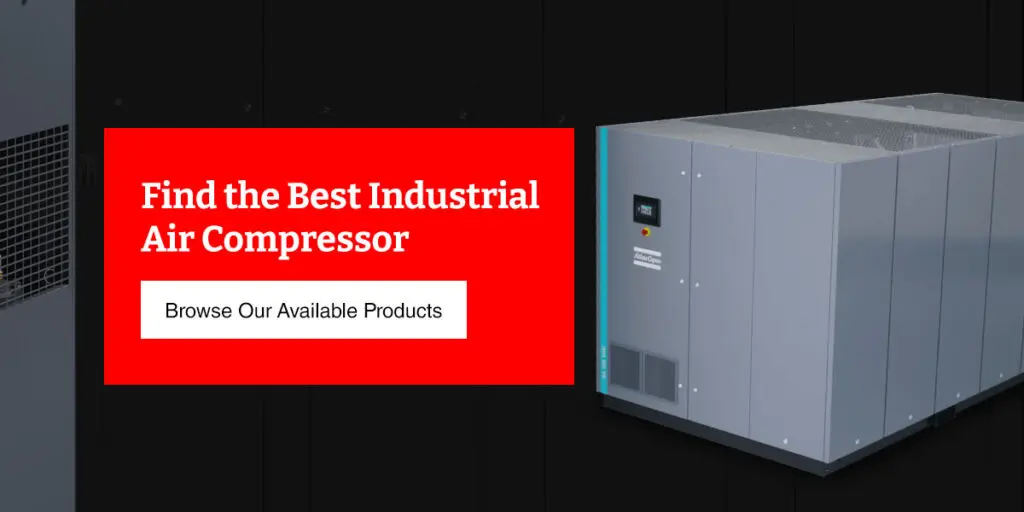
Find the Best Industrial Air Compressor
Industrial Pneumatic Systems is your full-service air compressor company. Our team makes it easy to find compressed air solutions that meet industry demands with efficiency and reliability. With more than a decade of experience and a knowledgeable team, we can help you choose lasting solutions, whether you work in the healthcare, automotive, manufacturing, production, food, or municipal sector.
Find a high-quality air compressor for industry applications. Browse our available products or request help to find the right one for your needs.